このページは我が社の本業務とは少し離れた内容です.こんなことを技術開発できたらいいなと日々考えていることを具現化していきます.成形技術から一歩踏み込んだ領域です.
1.コンプレッション成形機のデジタル制御化
なぜデジタル制御化したのか?
以下の2つが理由です.
1.制御装置が古くなったから.
現在,コンプレッション成形機はアナログ部品で制御されていて,デジタルな部品が一切ありません.当然,制御精度もそれなりの精度となります.でも,制御対象もアナログな構造(油圧バルブを開閉してシリンダを上下に動かす)なので,お似合いの組み合わせです.これはこれでいいんです.あとは操る人間が成形機の特性を分かった上で動かせれば.
しかし,ここで問題が.制御対象は非常に丈夫に出来ているのですが,制御装置の電子部品はそれに比べて丈夫なものではありません.
今回試験機となる成形機は我が社に中古でやってきて30年.油圧機械そのものにはなんの不具合もありませんが,タイマーやスイッチなどの電子部品が故障しはじめました.
2.成型工程を複雑化するため.
現在のアナログ制御では以下のような製造工程を制御します.
a.予熱(金型に投入した材料に熱を加えるため,0圧型締めを行い,一定時間保持します.)
b.ガス抜き(低圧型締めを行い,一定時間保持した後,型開きを行い型内のガスを抜く)
c.圧縮成型(高圧型締めを行い,一定時間保持し,材料を製品形状へと圧縮成型する)
上記3工程を順を追って行います.単純形状の製品ならこの3工程で良品を簡単に成型できます.しかし,複雑な形状の製品や,インサート成型の製品などはこの3工程だけでは良品を成型できない場合があります.ここが他社との違いかもしれません.一般的には成形工程は上の3工程で行うのが最も良いとされ,過不足はないと考えられています.これ以上の成形工程の追加・削減は生産効率を落とし,不良率の増加を招くと言われているようです.
私たちは予熱工程に多少の細工を施し,ガス抜きの工程を複数回繰り返すような制御が欲しいと考えていました.
デジタル制御装置
以下のような部品で制御装置を構成しました.
1.パソコンで制御できるAD/DA変換器
2.SSR
3.圧力・変位センサ
4.パソコン
AD/DA変換器で複数のSSRを制御することで,各アクチュエーター(各油圧ソレノイドバルブ,油圧ポンプモーター)の電源を制御しました.
AD/DA変換器はVisualBasic.NETで作製したWindows用アプリケーションソフトで制御します.
作製した制御画面は下図のようなものです.
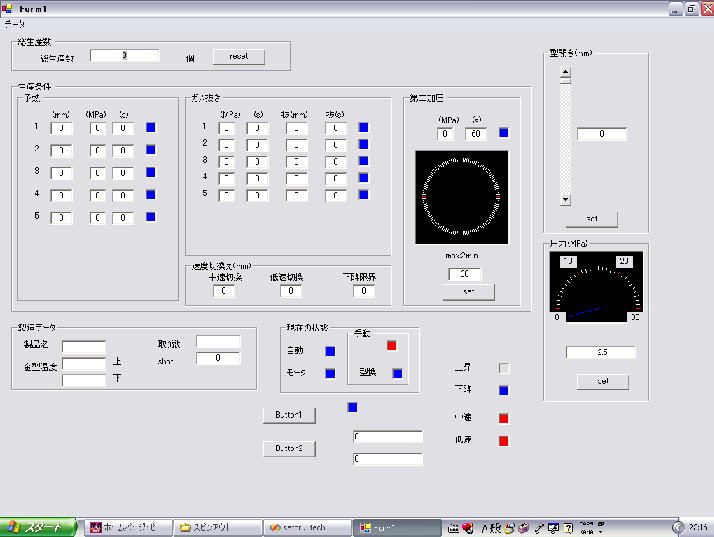
図(制御画面)
画面が見にくいかもしれませんが,printscreenでコピーするとこの画面が精一杯です.
詳しい作製法などはそれに関する本や,ネットの情報で流れているので,あえてここで紹介する必要はないと思います.私はVisualBasic.NETを初めてプログラミングしましたが,とても分かりやすく,使いやすいツールだと思います.
インプレッション
まぁまぁ思いどうりに動きます.不満な点は各センサーから返ってくる信号に対して応答が遅れているということでしょうか?考えられる原因は2つあります.1つは各アクチュエーターの応答がどの程度なのか仕様書がないので応答速度の調整は大体になること.もう一つはパソコンの信号発信タイミングは本当にプログラムどうりなのか?この辺はパソコンを用いた制御の泣き所だと思います.パソコン自体がどの程度の優先順位で時間管理をしてくれているのかはパソコンメーカーかインテ○かマイク○ソフトしか知らないので,調整はある程度大雑把にならざるを得ません.私が作製した制御プログラムではサンプリング周期を100msecより小さくするとアプリケーションがフリーズしてしまいました.
実際の制御誤差は変位で2〜10mm,圧力で0.5〜2MPaほどです.ここら辺を変位+-1mm,圧力+-0.5MPaに収めることができれば程よいと思います.今のところプログラム側で応答遅れを見越した偏差を組み込んでいるので肝心なところで大きく誤差がでないようになりました.
成形製品に与える影響についてですが,良品の成形をしやすくなるという効果を得ました.どういったことから良品を成形しやすくなったのか,以下の2項目に分けて述べようと思います.
1.予熱
予熱とは油圧が掛からない程度の型閉めをし,材料に熱を加える動作のこと.その目的は材料に熱を加えることで材料を軟化させることです.軟化した材料は流れやすさを持ち,加圧工程で成形しやすくなります.
しかし,熱硬化性樹脂は軟化後,更に加熱すると硬化するという特性があるので,予熱時間には限界があります.通常は硬化する前に加圧工程に移行すれば良い話ですが,材料の量や製品形状によってはこの予熱の掛け方では不十分です.特に材料の量が多い場合,金型に接触した部分は熱が伝わりますが,内部には伝わらない場合が考えられます.このまま加圧工程に進んでしまうと,材料の一部に粉末の流れ特性を持ったままなので,製品の一部が材料不足のような不良品ができあがります.また,製品形状が複雑な場合も同様に,材料に粉末の流れ特性をもったまま加圧してしまうと,材料不足の症状,または,金型内にピンなどが有る場合はピンの破損などの原因になります.
これらの不具合(実際に起こった事例です)を改善するため,パソコン制御では予熱にシリンダの微上昇動作をさせました.一番良い方法は予熱をしている間に加圧しない程度にゆっくりシリンダ上昇させることなんですが,これは制御というより油圧回路(ハード)側にアクチュエーター(フローコントロール)を追加しないことにはできないので微上昇動作という結論になりました.
予熱中に微上昇動作を行うことで軟化した材料を金型内の空いているところに流し,熱の伝わっていない材料に金型を接触させることができるはずです.現に前述した不具合は改善されました.
2.ガス抜き
ガス抜きとは,成形中に材料から発生したガスを型開きして抜く動作です.熱硬化性樹脂は成形中にガスが発生します.このガスを上手く抜かないと製品の内部にガスが残存してしまい,風船のように膨らみます.単純に加圧成形を途中で減圧し,型を開けばガスが抜けるのですが,アナログ制御の1回では抜けきらないことが多いのです.また,ガス抜き前にどのくらい加圧するのかも問題で,製品形状によっては低圧(5〜15MPa)を用いたり,一気に20MPaまで加圧してガス抜きを行ったりとパターンは様々です.
このガス抜きの回数やパターンを多くすることでガスが製品に残存することはなくなりました.
特に予熱の部分にはこだわった部分があるので長くなってしまいました.もともと,予熱に上記のような動作を加えるようというのがこのデジタル制御化の発端なので,当初の目的は達成したと思います.
今後の発展
一応の完成を納めたわけですが,思うところは多々あります.まず,制御装置にパソコンを用いるのはどうなのかというところです.上述した”正確さ”というのもありますが,現場で使用することを考えると,パソコンにとって劣悪な環境(汚れや,成形時に発生するガスにさらされる等)で使用することは後のトラブルを招きかねないのではないかと思います.
また,コストパフォーマンスについてもパソコンを用いると”手ごろ”ではなくなります.
かといって,利点がないわけでもありません.自動制御中に成形条件の書き換えができること(run中書き換え),プログラミング変更が簡単なこと,成形条件をtextファイルで保存できること.使い易さでは今が一番のようです.
現在考えているのはワンチップマイコンでパソコンの代わりをさせることです.しかし,この場合,run中書き換えは出来ませんし,成形条件も一つしか記憶できない上に,書き換えは100回が限度となってしまいます.もう少し勉強してから取り組みたいと思います.
成形(プレス動作)が自動になったので,材料投入や製品取り出しを自動化できれば立派な自動成形機となります.今後は材料投入・製品取り出し機構・制御も考えていこうと思います.
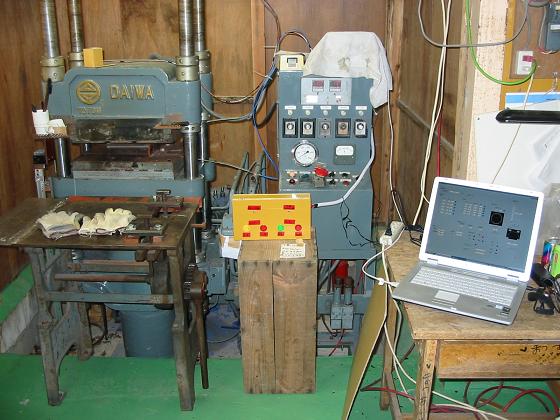
装置完成図
図(制御装置を取り付けた図)
制御装置をコンプレッション成形機に取り付けた状態です.昔ながらのアナログ制御盤も残してあります.(パソコンを接続してない状態ならアナログ制御も可能)アナログ制御盤の上の布をかぶせた箱がAD/DA変換器とSSRです. 布は埃よけにかぶせました.スイッチボックス(画像中央の黄色い木箱)を追加で作成しました.
※その後も続けて使用しておりますが,制御によるトラブルはありません.3つの製品をこの生産機械で生産していますが,扱いづらさ等も発生することなく使用しています.誰でもボタン1つで成形に取り掛かれるので,担当以外の人間が取り掛かるのに障害がないというのもメリットの一つかと思います.
ただ,制御を細かく設定できるようになって感じたことは,成形をよく理解していないと制御装置を使いこなせないということです.成形条件さえ合ってしまえばボタン一つなのですが,その成形条件を出すのに間違った条件では永遠に良品は得られません.
3年が経ちましたので,そろそろ制御に信頼もおけるので,周辺機器(材料投入・製品取り出し機構)を開発する気になります.考えてみようと思います.
'10,7,8追記
この制御装置を開発,設置してから約3年が経ちました.これまで大きなトラブルなどなく,通常の生産に使用しております.私としてはトラブルがあった方が面白いのですが,現場で使うものとして設計したので,期待を裏切っております.ただし,トラブルがないからと言って何もしないわけでもありません.
上記の開発後記で”パソコンを使用するのはコストパフォーマンスが悪い”と書きました.私としては新しいパソコンでなければ制御できないというアプリケーションソフトを開発したつもりはないので,中古のパソコンとそれまで使用していた新型パソコンとを入れ替えることを考えました.最近では中古のパソコンがOS付きで2万前後で買えるようですし,コストを抑える意味でやる価値はあります.しかし,ここからが大変でした・・・.
少しプログラムについて書きます.新型のパソコンと中古のパソコンで,ソフトの動作はできるのか?という単純な疑問が湧きます.弊社に来られたお客さまの中でも,自作パソコンプログラムはパソコンが変わるとプログラムは動かないから汎用性が低いと言われた方もおられました.ここからはマイクロソフトの宣伝のようになりますが,VisualBasic.NETからはある程度汎用性があると言えます.特に,パソコン(ハード)の違いというよりも,OSの違いに強いといえます.なので,開発に使用したパソコンと同じハード仕様ならば,.NETFrameworkのインストールで確実にソフト動作はできます.さて,ここまでがマイクロソフトの宣伝どおりのことを書きました.
ここからは現場の判断を書きます.来客された方の言葉の真意ですね.プログラム上,どのOS(ここではwin2kからwinXPあたりまで)でも動作します.なので,旧世代のハード(pentium3)あたりでも動作するように錯覚します.本当に微妙なところですが,プログラムで負荷のかかるもの(グラフィックやタイマーコントロール)などはその世代のハードに則した量しか取り扱いできません.なので,私の場合,pen3の中古パソコンを用意しましたが,celM1.3のパソコンで動作したソフトが動きませんでした.いくつかのグラフィックプログラムを削除して,タイマーコントロールの量も同時カウントなどさせないように調整することでpen3でも動作するようになりました.これで中古のパソコンで生産機械を動作させることができるようになりました.
が,制御のスペックを多少スポイルしているとも言えますね.また,ここまでできるようになるまでに知り合いから違うスペックのパソコンを何台も借りたり,自分でも中古パソコンを1台別に購入したり余計なコストが掛かってしまいました.それでも新型のパソコンよりは安いですが.
今回の変更点
パソコンを中古パソコンに入れ替え.
プログラムを旧世代のcpuでも動作するように組み替え.
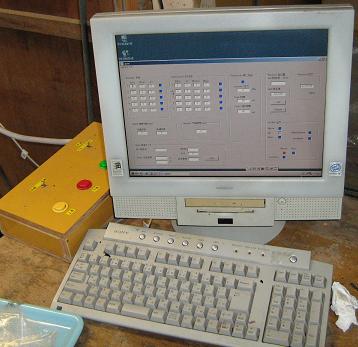
成形製品例
フェノールの箱状の製品です.インサート部品が計14箇所あります.全て一つずつ手作業で型内に挿入します.
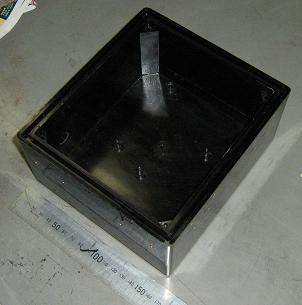
大きさが185×165×95mm,肉厚が約15mmと大きめの製品です.重さは1.3kgあります.予熱,ガス抜き共に長い時間と工程数を繰り返す必要があります.プログラムで用意した工程数を全て使って成形条件を出しました.
予熱に合計で1分半,ガス抜きを4回と約1分かけて,加圧焼成を15分程度かけました.立ち上げ量の大きい製品なので,条件出しの半ばで製品の胴体が材料切れを起こしたり,底面が材料切れを起こしたりとなかなか厄介でした.
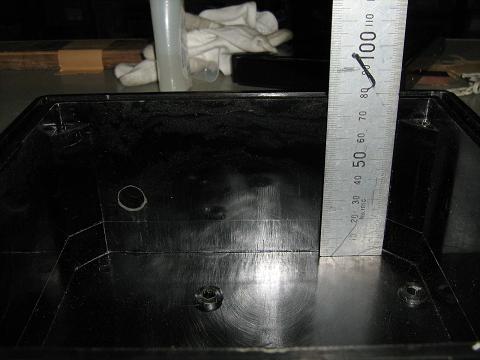
投入後,平らな材料をコア型でゆっくり押しつぶしながら写真のように80mmまで立ち上げでいきます.そこで厄介なのがガスです.立ち上げる動作をしながらもガスは発生してきます.うまいタイミングでガス抜きをかけていかないと,ガスだまりや前述した胴切れを起こします.
今回,この製品を自作した制御装置で成形したのには理由があります.それは各工程の時間間隔が数十秒単位と長いということです.手動で人間が管理するとなると,時計の秒針を見ながら大雑把に動かすことになります.また,あまり間隔が長いと成形担当の人間の集中力が切れる恐れがあります.
もし不良品をだせば14個のインサート品と1.3kgの材料が無駄になります.
現在では成形条件も決まり,ほぼ成形上での不具合はありません.材料を無駄にすることもなく,環境にも優しいですね.